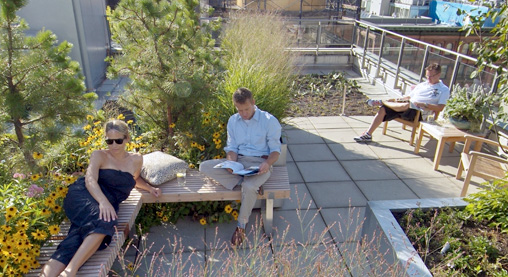
ZinCo develops “Natureline”, a system build-up made from renewable raw materials
Press release, 26 August 2013
|
The name ZinCo has been synonymous with innovation and sustainability for many years now. As a pioneer in matters of green roofing, ZinCo has been consistent in treading the environmental path for over forty years. Providing permanently reliable green roof systems for all types of roof, our top priority is to do so in an environmentally-compatible way. ZinCo system substrates, therefore, are based on recycled, pure-grade clay brick. Where possible, recycling materials are also used for drainage elements and protection mats. ZinCo has now taken yet another innovative step. On the occasion of the 3rd International Green Roof Congress in Hamburg in May, ZinCo introduced "natureline", the system build-up made from renewable raw materials. Why renewable raw materials?In a time of increasing scarcity of fossil raw materials and of global warming, ZinCo has taken on the resulting challenge and is looking for suitable solutions for conserving natural resources. The use of renewable raw materials is an obvious solution and one that promises huge potential. Renewable raw materials are biomass sources from agricultural, forest or marine production. They are typically one or two-year old plants such as grain, maize, sugar cane, oleaginous crops, wood and in the future possibly even algae. Mankind is exploiting the advance work of nature here, for example as carbon is extracted from the atmosphere in the form of CO2 through the process of photosynthesis and is converted to energy-rich, organic compounds (biomass). The resulting sugar and other elements can be used as energy sources or chemical raw materials, for example for the production of bioplastics. Bioplastics are plastics that are created on the basis of renewable raw materials. A biomass is generally converted to plastic using a multi-phase (bio) chemical-technical process. There are many different bioplastics, including mass plastics (e.g. PE, PET), technical plastics (bio-based polyamide, PUR) and new types of plastic (PLA, PHA). The figures speak for themselvesIn theory, 90 % of all plastics could already be produced today from biomass instead of from petroleum but, in practice the production figures show a very different picture. For example, in 2011 less than 1% of the overall global plastics production was biobased. However, the annual growth in production is at least 20 % (without subsidies). Source: https://www.european-bioplastics.org/ At the moment, production costs for bioplastics are higher than those for the fossil plastics that are to be replaced, but the trend is towards a continually improving cost-effectiveness. It must also be mentioned that the price of renewable raw materials and bioplastics continues to drop, while, as is well known, the price of crude oil is still rising. The decisive advantage of renewable raw materials compared with fossil raw materials is that they contribute to reducing the glasshouse effect and therefore play a role in climate protection. For example, when bioplastics are compared with fossil plastics (based on comparable applications) the savings in CO2 emissions are generally speaking between 20 % and 80 %. In addition to the parameters "CO2 emissions" and "conserving fossil resources", there are other factors that are significant when evaluating bioplastics. Not all aspects of bioplastics are basically better but they do fare extremely well with regard to highly-weighted factors. In addition, there will be a plus in the life cycle analysis once special residual and waste materials can be applied as raw materials. The ZinCo focusZinCo developed the idea of a green roof system based on renewable raw materials together with Tecnaro GmbH, a pioneer in the field of biobased materials. Tecnaro GmbH has been very successful in the field of bioplastics since 1998 and at the Hannover Trade Fair in April was awarded the international GREEN BRAND Germany, among other things for the materials group ARBOBLEND. One type of material from this group was developed specifically for use with thermoformed applications such as drainage elements and it shows properties that are comparable with those of conventional polyethylene. With Tecnaro, ZinCo has found a partner who shares a common approach in terms of the requirements of quality and environmental sustainability. The drainage element in the "natureline" system build-up is produced mainly using sugar cane, the most efficient and largest capacity sugar plant worldwide. The process energy required to convert sugar to plastic is also drawn to a great extent from biomass. Sugar cane is grown in line with strict statutory requirements that take into consideration both social and environmental standards and the protection of nature (recognised as per EU biofuel regulation). The raw material is farmed and processed in the Federal State of Sao Paolo, about 2,000 km from the Amazon rainforest. The protection mat and the filter mat in the "natureline" system build-up consist of PLA (polylactic acid). This bioplastic is created through the polymerisation of lactic acid, which is in turn a product of the fermentation of maize starch using lactic acid bacteria. One important advantage of PLA is the special diversity of this bioplastic, which can be adapted to be quickly biodegradable or to be permanently viable. Further advantages are its strength, thermoplasticity and its good processing characteristics on existing machinery in the plastics processing sector. A holistic viewAny decision to start using bioplastics is taken in the full knowledge that renewable agricultural raw materials are only available in limited supply. Agricultural land serves many purposes, in particular the cultivation of foodstuff. Given a usage of only 0.006 % of the agricultural land worldwide (source: European bioplastics and IfBB Institut für Biokunststoffe und Bioverbundwerksstoffe), we are certain of one thing at ZinCo: The development of bioplastics and of sustainable concepts that are based on them, for example, green roofing, is the right way to go. The potential offered by bioplastics is in no way exhausted. Algae or agricultural residual materials may be used in their production in the future. The long-term goal is a bio-economy in which fossil raw materials and energy sources are replaced by renewable raw materials without affecting livelihoods. Thanks to the system build-up "natureline", bioplastics have now found their way onto the green roof market where they will prove themselves as an alternative with a promising future. Author: Dieter Schenk, Managing Director ZinCo GmbH For further information, please contact:
|